Innovative Connectivity Solution for Disruptive Wind Propulsion Technology
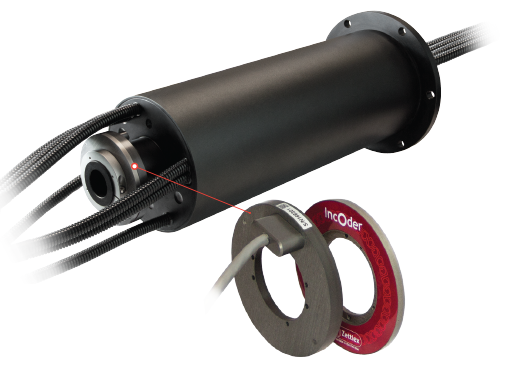
Climate change context pushes industrial decision-makers to turn towards sustainable technology models in terms of production, development, or transportation. We have seen many improvements in that field in the car industry with the rise of hybrid cars then electrical ones. But some interesting developments are made in maritime transportation too. This is the case of the Oceanwings® designed by the naval architects of VPLP that has been brought to an industrial model in collaboration with CNIM. PES S.A. has participated in this innovative project since the beginning providing a standard slip ring for the set-up of a demonstration prototype and then a highly customized solution for the system that is now installed on the Energy Observer vessel.
Oceanwings® is a fully automated wingsail, enabling hybrid propulsion featuring a mix of wind power and conventional propulsion. To enable automation, the mast embeds a lot of technologies such as strain gauges, thermocouples to monitor the structure and environment but also servomotors to perform sail maneuvers. The wind propulsion concept created by VPLP allows the wing to be automatically positioned depending on the wind direction in order to benefits from the maximum performance of the system, all the time.
Thus, this means the mast can rotate continuously depending on wind and boat directions. This has been made possible through the use of a slip ring that is installed in the mast that allows the transfer of servomotors power and feedback, monitoring sensors signals but also Fieldbus communication between the rotating equipment on the mast and the controller. This way Oceanwings® can perform smooth and reliable operations enhancing the energy efficiency of the boat and comfort of sailing operation.
Moreover, an absolute encoder was also needed in order to retrieve the mast position in real-time which is very important information for the automation algorithm. PES S.A. has adapted the slip ring design and provided a mounting interface for direct encoder integration allowing easy integration of the slip ring/encoder assembly into the mast.
Electrical Features
- Motor power and control through specific cables
- Automation component supply and signals (I/Os, EtherCAT, Ethernet, Profinet, CANOpen, etc.)
- Sensors (low voltage signals transmission: strain gauge, thermocouples, etc.)
Mechanical Features
- Low friction torque
- Customized mounting options
- Compact size
Interesting Options
- IP65 for the maritime environment
- Integrated proprietary cables
- Integrated large thru-bore encoder
- Combined with hydraulic rotary union for high actuation power
Advantages
- Long lifetime without maintenance
- Reliable continous rotation
- Highly customized solution (cable length, encoder integration, circuits, IP65, etc.)
Benefits
- Enhance the Total Cost of Ownership by avoiding difficult access maintenance operations
- Optimize Oceanwings® performances and simplify the automation algorithm
- Save on integration and installation costs
Facts & Figures
- With a medium speed of 5 rpm a slip ring (multi-wire brushes design) can operate at least 20 years without being replaced
- Power signals and sensors or control signals (Field bus, motor encoder, etc.) can be embedded in the same slip ring
- Oceanwings® are now proven-in-use in very harsh environmental conditions, Energy Observer has joined the Spitzberg and crossed the Atlantic Ocean giving Oceanwings® thousands of miles of operation