Proven-in-Use Robot Welding Gun Changing Solution
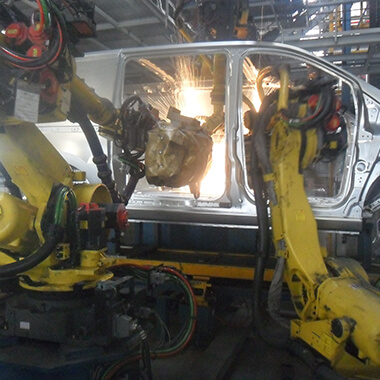
Flexible welding lines that we find in the automotive industry shall take up minimum floor space and then requires a single robot to often handle several welding guns.
The welding gu in itself is a concentration of technology, it embeds servo control of position and strain, the welding power and all the electronics and sensors needed to enable automation of the equipment. We then find 3 kinds of energy: the electrical power, the pressurized air, and the coolant.
When it comes to using a tool changer in this context, all the necessary information and energies have to be transferred through the tool changer.
PES know-how is well-known in the automotive and other industries in creating customized modules for quick-coupling of fluids, electrical signals, and power in order to meet the robot tool needs.
We also developed specific docking stations for welding guns that include a protective cover to prevent pollution or dirt. This station also integrates 3-axis compliance that assures a tool docking and picking quality whatever the material wear and this within minimum cycle time.
This functionality can adapt to every robot available on the market as well as every well-known welding guns manufacturer.
Electrical Features
- Quick connection of motors (power and control)
- Quick connection of Field Buses or discrete I/Os
- Tool presence and docking monitoring
- Output voltage power-cut before docking
- Tool changer status control and monitoring through discrete I/Os or Fieldbus
Mechanical Features
- Cam lock mechanism with integrated wear compensation
- Tough design for payloads up to 800kg and more
- Custom robot and welding guns interface available
Interesting Options
- Tool coding
- Docking station with a compliant fixture
- Tool protection cover for dusty environments
Advantages
- Standardization of mounting fixture
- 3-axis Proven-in-Use compliant docking station
- Wide range of quick connection available and Proven-In-Use
Benefits
- Cost of tooling peripherals reduced
- Integration costs and project risks mitigated
- Limited maintenance costs
- Limited development costs
Facts & Figures
- With a good integration, tool change can be performed in less than 5 seconds
- Cam locking mechanism can outreach 5 millions of operation cycles
- PES Tool Changing Solution complies with Level-D safety performance level requirements
- PES is a leading supplier of tool changing systems in the automotive industry worldwide for more than 20 years with hundreds of units in operation
- PES has extensive experience with most of welding guns manufacturers (ARO, FTS, Obara, Comau, etc.)