Robot Manual Tool Changers | Medium Payload | MGW160
The Universal MGW Connector - Safer and more precise tool changer for your applications.
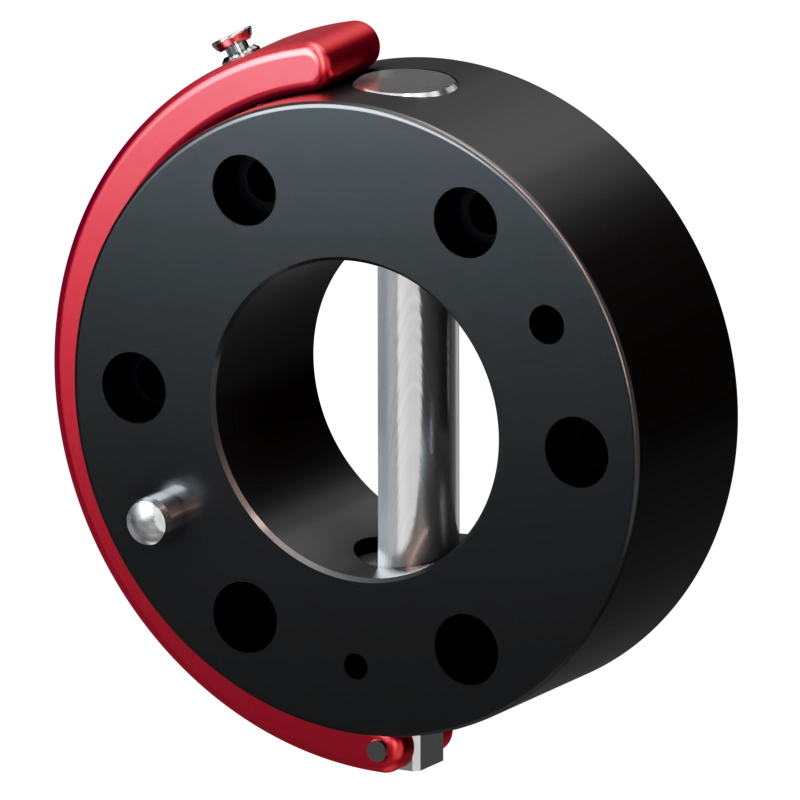
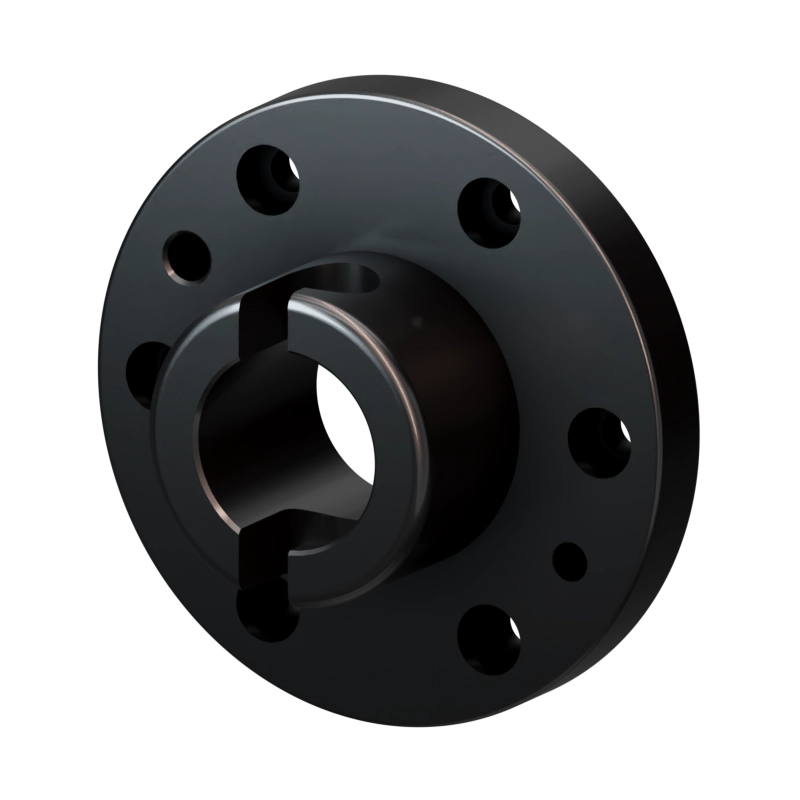
The new MGW Connector is our universal quick changer for every application. The new system is of higher quality and offers more safety and accuracy. The innovations are a response to the current requirements of our customers. A centering disc can be installed on both the upper assembly (robot side) and lower assembly (tool side) of the robot and ensures that the tools are correctly aligned with the robot arm.
Advantages
- Withstands high loads with low dead weight
- Can be released and closed with one handle
- During locking, the lower assembly is pulled around the locking stroke
- Interface according to DIN EN ISO 9409-1
Benefits
- Does not require a deep review of the echanical structure to be integrated.
- Cost savings through reduced maintenance downtime.
- Improved equipment versatility and upgradability and then extended productivity.
- Mitigate the need of specifically designed mounting interfaces