Collision Sensor | medium payload | QS-200
Collision detector QS-200: Protect your equipment in demanding environments
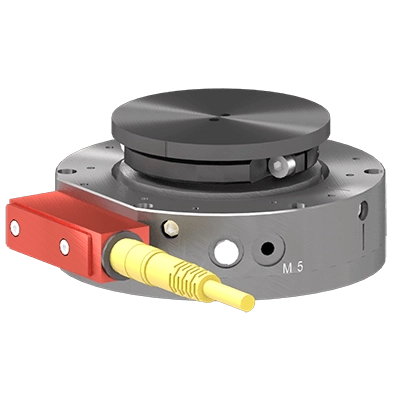
With moments trip point from 7.5 to 290 Nm, medium payload collision sensors will be the most appropriate models for your applications such as cutting or gripping.
- Dynamically variable collision sensor that operate on air pressure. Breakaway threshold adjusts to match the working force ranges of robot/application
- Non compressive, metal to metal seal for reliable and consistent operation
- Opening of QuickSTOP air chamber at impact, pressure exhaust and switch signal stop the robot
Advantages
- Senses angular and compressive forces. QuickSTOP’s unique design offers protection in X, Y and Z axis
- Linear and angle strokes available to remove the forces from end of arm tooling and robot wrist at trip point
- Performance readiness is monitored by QuickSTOP. When pressurized, the switch indicates that the QuickSTOP is reset in proper position
Benefits
- Minimize down time, quick reset, no need for recalibration, stopping robot at source of impact allows for easy identification of cause
- Minimize robot and expensive end of arm tooling damage during robot programing. A must for any education or robot training cell
- Easy to implement, simple to adjust pressure level according application, quick return on investment